In today’s rapidly evolving eCommerce landscape, it has become extremely important for businesses like yours to adapt and rethink your warehouse management strategies.
Fulfilling customer orders while staying profitable demands more than just hard work; it requires a blend of innovation and a proactive approach to problem-solving.
To implement innovative solutions, you must be aware of the challenges and complexities that come along with managing a warehouse.
Let us look at the story of Shagun and Sarthak to understand primary warehousing challenges and the solutions they implemented to run their business like a pro.
Story Unfolds
At NovaTrade’s lively headquarters, a fast growing eCommerce company, two key team members are working together to tackle the complexities of global eCommerce warehousing. Shagun, the logistics director, is an experienced leader known for her practical solutions and sharp focus on results. By her side is Sarthak, a young and enthusiastic supply chain analyst fresh out of grad school, bursting with innovative ideas on how technology can solve their biggest challenges.
The duo is committed to tackling the company’s biggest warehousing issues and paving the way for sustainable growth. Their story reveals the most pressing challenges in global eCommerce warehousing and offers actionable solutions to stay ahead in 2025.
Key Challenges in Global eCommerce Warehousing
Demand Volatility
Over the weekend, a viral social media campaign caused sales to skyrocket. By Monday, Shagun’s inventory reports were showing stockouts for several key products. The unexpected demand spikes made forecasting feel like an impossible task.
Seasonal sales and unexpected surges due to viral trends create significant fluctuations in demand. This unpredictability makes inventory management complex, often leading to either overstocking or stockouts.
Geographical Distribution
As NovaTrade expanded into South America, Shagun struggled to maintain quick deliveries to remote areas. Customers were frustrated by delays, and costs were climbing.
Strategically located warehouses play a key role in ensuring timely delivery across global markets. However, maintaining facilities in diverse regions comes with logistical complexities, regulatory challenges, and high costs.
Integration with Global Supply Chains
Delays at customs and communication breakdowns with international suppliers created bottlenecks that slowed order fulfillment.
Coordinating with suppliers, manufacturers, and distributors across various countries and regions involves navigating customs regulations, language barriers, and varying technological standards.
Labour Shortages
Seasonal peaks overwhelmed the local warehouses, leaving them short-staffed and overworked.
While the demand for skilled labour in eCommerce warehousing operations continues to grow, maintaining productivity in physically demanding roles is a challenge.
Technology Adoption
Warehouse teams resisted new tools and technologies, fearing it would complicate their jobs instead of making them easier.
Adoption of technologies such as robotics, AI, and IoT requires significant investment, training, and a cultural shift within organisations.
Sustainability Pressures
NovaTrade’s customers were increasingly vocal about their expectations for greener, more eco-friendly operations.
Moreover, with government pushing for sustainable practices, warehouses must reduce their waste generation, lower energy consumption, and adopt eco-friendly packaging materials to stay competitive.
Rising Operational Costs
Rising utility bills and transportation costs were squeezing profit margins.
From real estate and utilities to labour and transportation, the cost of running a global eCommerce warehouse has been continually rising.
Last Mile Delivery Challenges
Urban congestion and limited rural infrastructure made it difficult to deliver orders on time.
Efficient last mile delivery depends on the warehouse’s proximity to the end consumer.
Inefficient Returns Processing for Reverse Logistics
After a major sales event, Shagun noticed a significant backlog in processing returned goods. Customers were frustrated by delays in receiving refunds, and warehouse shelves were cluttered with unprocessed returns.
Issues with processing returned goods can lead to inventory issues, create operational strain, as well as impact customer trust.
Managing Hazardous Materials
During an internal audit, Sarthak discovered gaps in the safety protocols for handling hazardous materials stored in the warehouse. Shagun knew they needed a comprehensive system to address these risks before they escalated.
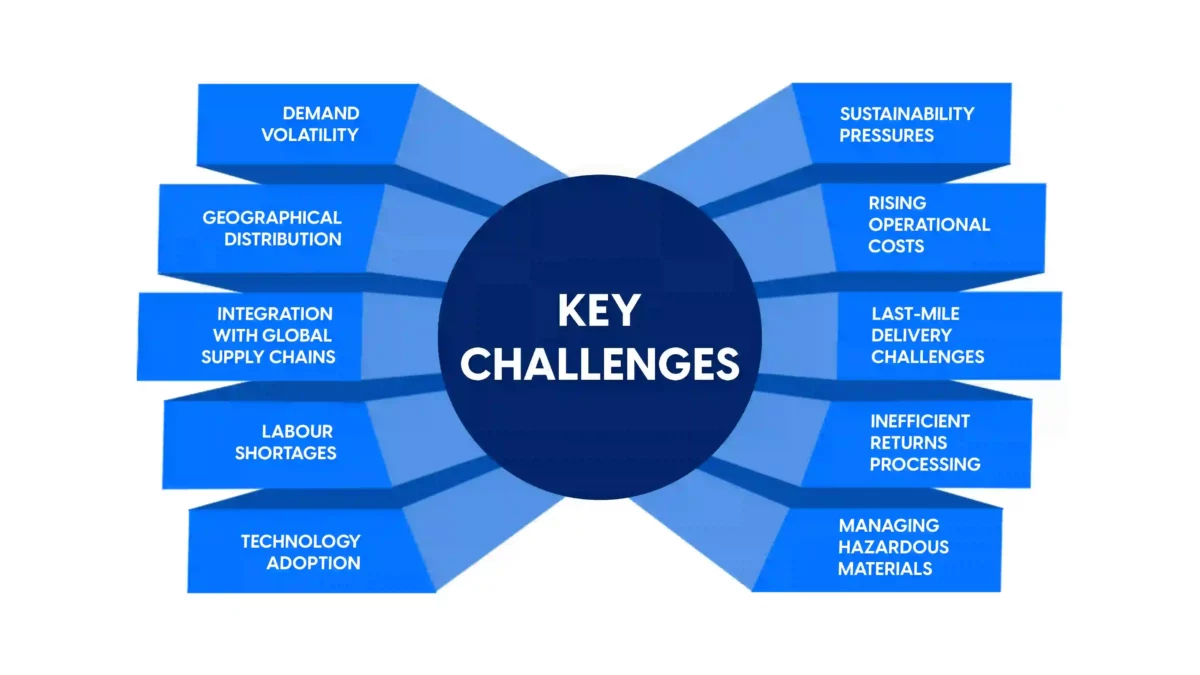
The Solutions
Demand Forecasting Using AI
Sarthak suggested using advanced AI tools to analyse trends and predict future sales patterns. By the end of the week, Shagun approved a pilot program that stabilized inventory levels and reduced costly stockouts.
IoT and RFID-based real-time inventory monitoring for the win.
Strategic Warehouse Placement
Using geo-mapping and data analytics, NovaTrade identified optimal locations for new warehouses in South America. These efficient distribution networks reduced delivery times and operating costs.
They analysed their business needs to decide which warehousing strategy will suit their business model- centralized or decentralized warehousing.
Blockchain for Supply Chain Integration
Sarthak introduced blockchain technology to improve transparency and efficiency. Real-time tracking and automated customs documentation smoothed out cross border delays.
Automation to Tackle Labour Shortages
Robotic picking systems and automated storage solutions transformed NovaTrade’s warehouses, improving speed and reducing reliance on manual labour.
Embracing Technology Through Training
Shagun hosted workshops and open discussions to ease the team’s transition to new technologies. With better understanding and support, adoption rates soared.
Green Warehousing Initiatives
Solar panels, reusable packaging, and rainwater harvesting helped NovaTrade’s warehouses become carbon-neutral. Customers took notice, boosting brand loyalty.
Collaborative Logistics
Sharing warehousing space with other businesses reduced costs and optimized resource utilization, particularly in smaller regions.
Improved Last Mile Delivery
NovaTrade tested drones and micro-fulfillment centers, solving urban congestion and rural delivery issues. Customers loved the faster service.
Streamlined Returns Processing
Sarthak proposed setting up a dedicated returns processing area within the warehouse, complete with trained staff and tools for inspection, repackaging, and restocking. He also recommended integrating returns management software with NovaTrade’s existing WMS to automate the process. Within weeks, the backlog cleared, refunds were processed faster, and customer satisfaction improved.
Hazardous Materials Management
Sarthak spearheaded the implementation of a Hazardous Materials Management System (HMMS), ensuring compliance with regulations for labeling, storage, and handling. Specialised storage solutions, such as flame resistant cabinets, were installed, and employees underwent rigorous safety training and emergency drills.
By 2025, Shagun and Sarthak envision a fully integrated, tech-powered warehousing network. Together, they’ve turned challenges into opportunities, creating a model of excellence for global eCommerce warehousing.
NovaTrade’s journey shows how strategic planning, technological integration, and a commitment to sustainability can help you thrive in the ever competitive eCommerce landscape.
Lessons from Industry Leaders
As NovaTrade innovated, Shagun and Sarthak drew inspiration from industry giants:
- Amazon’s Robotic Warehouses
Inspired by Amazon’s Kiva robots, NovaTrade implemented similar technologies to streamline operations and reduce processing times.
- IKEA’s Sustainable Warehousing
Shagun and Sarthak adopted IKEA’s approach to renewable energy and recyclable materials, aligning profitability with sustainability.
- DHL’s Smart Glasses
NovaTrade incorporated wearable technology to enhance picking accuracy and warehouse efficiency.
Summary Table: Key Challenges and Solutions
S. No. | Key Challenges | Solutions |
---|---|---|
1 | Demand volatility | AI-driven demand forecasting: set reorder points, use inventory forecasting and management tools |
2 | Geographical distribution | Strategic warehouse placement |
3 | Integration with global supply chains | Blockchain for transparency and efficiency |
4 | Labour shortages | Automation and robotic systems |
5 | Technology adoption | Training programs and open dialogue |
6 | Sustainability pressures | Green initiatives: solar panels, reusable packaging |
7 | Rising operational costs | Collaborative logistics with shared spaces; reporting and analytics tools to optimize costs |
8 | Last-mile delivery challenges | Drones; micro-fulfillment centers; automated shipment tracking |
9 | Inefficient returns processing | Dedicated returns area and returns management software |
10 | Managing hazardous materials | HMMS, safety training, and specialized storage solutions |
Conclusion
Efficient warehouse management is the backbone of any successful eCommerce operation.
However, if not handled well, warehouse challenges can disrupt workflows, impact productivity, and ultimately eat your profit margins.
From managing labourers efficiently to handling seasonal demand spikes and optimising space usage, the key to running a successful business lies in overcoming these challenges.
Use intelligent warehouse management systems to digitise different warehouse processes and improve efficiency. Tools for robust inventory management, multi-channel order management, and seamless integration with devices can help you serve more customers and grow revenue by increasing warehouse efficiency.
Just pick the solutions that suit your business requirements and be at the top of your game.
Happy Shipping!
FAQs
The major challenges include demand volatility, geographical distribution, integration with global supply chains, labour shortages, technology adoption, sustainability pressures, rising operational costs, last-mile delivery issues, inefficient returns processing, and handling hazardous materials.
Technology like AI for demand forecasting, blockchain for supply chain integration, RFID and IoT for real-time inventory tracking, and automation through robotics can improve efficiency, reduce costs, and streamline operations.
Regional fulfillment centres reduce delivery times by positioning inventory closer to customers, helping overcome geographical distribution challenges and improving last-mile delivery efficiency.
Warehouses should implement Hazardous Materials Management Systems (HMMS), train employees on safety protocols, conduct regular emergency drills, and use specialised storage solutions to ensure compliance and safety.